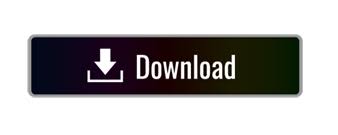
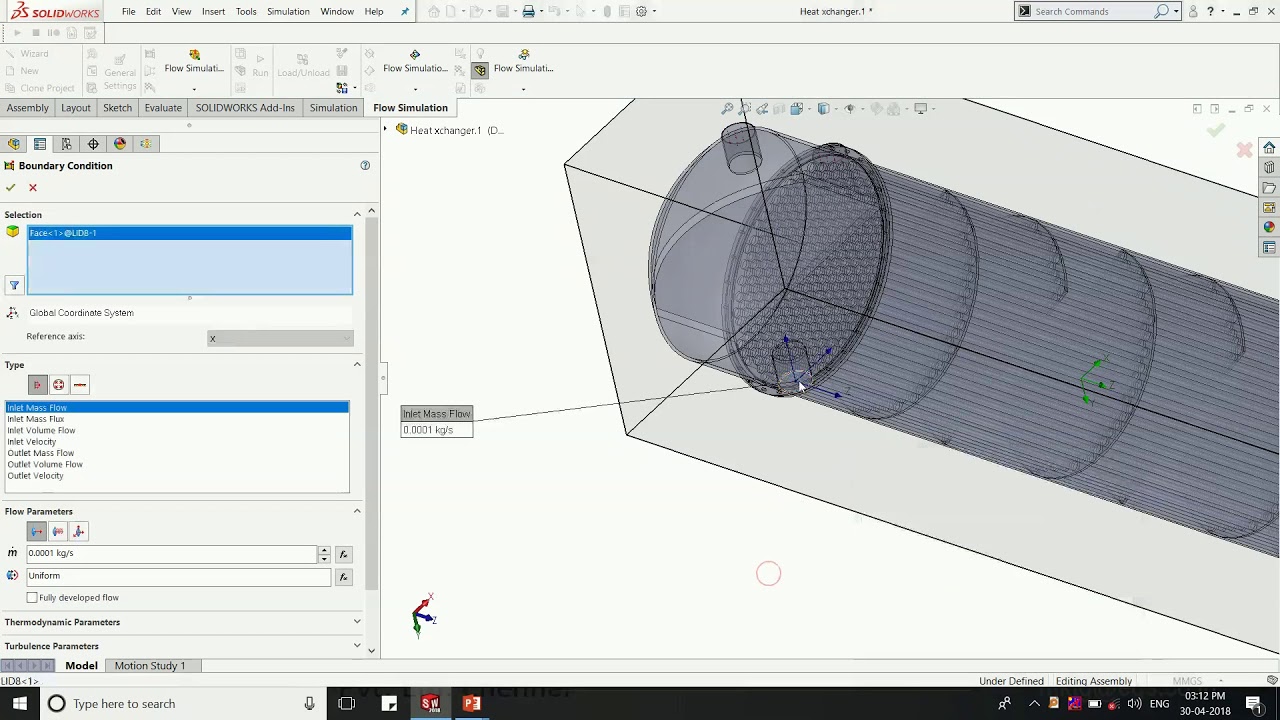
- SOLIDWORKS FLOW SIMULATION TUTORIAL HEAT EXCHANGER PARTY PROFESSIONAL
- SOLIDWORKS FLOW SIMULATION TUTORIAL HEAT EXCHANGER PARTY SERIES
- SOLIDWORKS FLOW SIMULATION TUTORIAL HEAT EXCHANGER PARTY FREE
You can clearly see how the forced convection of the fan is blowing over the heat sink resulting in higher h values, between 60-90 W/m 2K, and towards the rear the values drop down significantly to less than 20 W/m 2K.
SOLIDWORKS FLOW SIMULATION TUTORIAL HEAT EXCHANGER PARTY PROFESSIONAL
And as a result, the calculated temperatures using Simulation Professional Thermal solver appear to be more uniformly distributed than in reality.įor example, take a look at the local variation of convective heat transfer coefficient on the surfaces of a heat sink that is placed in front of a fan in Image 3.
SOLIDWORKS FLOW SIMULATION TUTORIAL HEAT EXCHANGER PARTY FREE
Trying to predict or estimate these values is a tedious task using tables or hand calculations, so we resort to simply using a range of values typical of free or forced convection. Note that h is highly dependent on several factors, such as surface orientation, velocity, wall temperature, wall shape, solid and fluid properties, surface condition and more. Even if the time and effort were taken to figure out an average value of h for every horizontal and vertical surface separately, it would still not be as detailed. There is no need to define the convective heat coefficient (h) and fluid temperature on wetted surfaces, as you would need to for Simulation Professional, because the Flow Simulation solver calculates it for you in a very localized way for each computational volume, or cell. But the good thing is that the user inputs can be as simple as setting the ambient temperature and pressure, and the amount of heat power, in Watts, dissipated by the component(s) in the design. It can take some time to solve a thermal CFD problem, perhaps a few minutes to a several hours depending on the complexity of the problem. The set of all these highly nonlinear coupled equations are iteratively solved for a given discretized geometry (or mesh) and boundary conditions (BC’s).
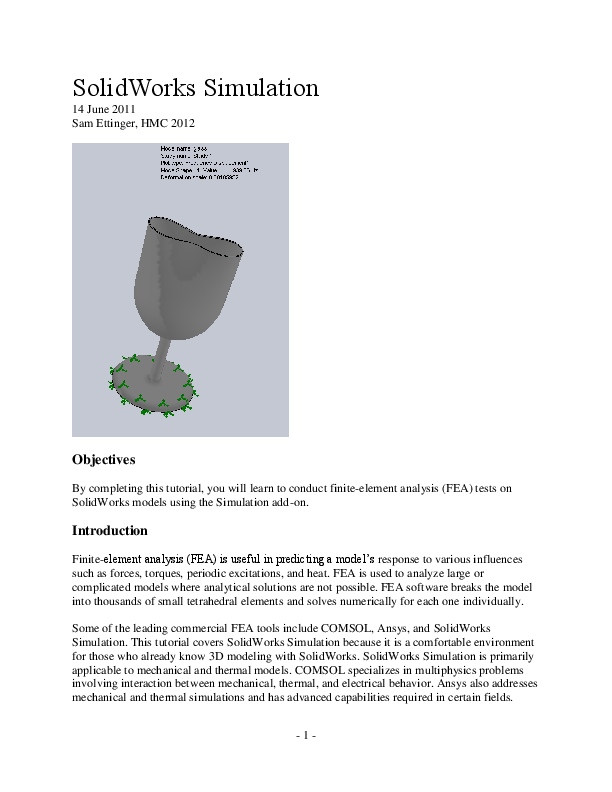
In other words, pressure, temperature, velocity and the fluid properties are all tightly dependent on one another. In more recent years with the subsequent advancement of computational analysis, a new approach to combine the heat transfer processes together was taken, so a “conjugate” heat transfer problem is combining any of the two (or all three) modes to be solved concurrently.įlow Simulation uses a Finite Volume (FV) method to solve the CFD equations, where three conservation methods (mass, momentum and energy) and the state equation are all maintained. Flow Simulation is better suited to solving conjugate heat transfer problems.ĭid you know that before the 1960’s, the process to solve conduction, convection and radiation was to handle them separately? As you might expect, this was not an accurate approach to solving the real physical process. I’ve made a long-form video explaining all of these modes in more detail, see link at the bottom, so I will only summarize them here in the series.Ģ.
SOLIDWORKS FLOW SIMULATION TUTORIAL HEAT EXCHANGER PARTY SERIES
The main 3 reasons why Flow Simulation is the better option will be outlined in a series of three parts.Īs noted above, there are three modes of heat transfer: conduction, convection and radiation.

The most typical exceptions would be when: (1) there is no convective heat transfer mechanism in the problem that is being solved because likely the object(s) are in a vacuum and only transport heat through conduction and radiation or (2) the thermal solution does not require a great deal of accuracy reflecting a physical test perhaps in the very early design stages when estimates are sufficient. With the exception of very few scenarios, when considering a thermal analysis solver for SOLIDWORKS, you should choose to use Flow Simulation, which is a computational fluid dynamics (CFD) code. For thermal heat transfer analysis, choose SOLIDWORKS Flow Simulation over the Thermal solver in Simulation Professional, Part 2 of 3 Conjugate Heat Transfer
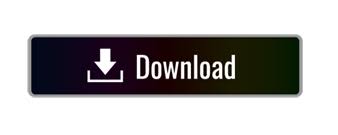